Galvanic treatments consist in electrochemically coating products with a thin metal layer, in order to improve both technical characteristics and appearance.
The Celsia factory, which specialises in manufacturing electrical contacts for medium and high voltage applications, has an extremely efficient plant that makes two types of these treatments: silver coating and copper plating.
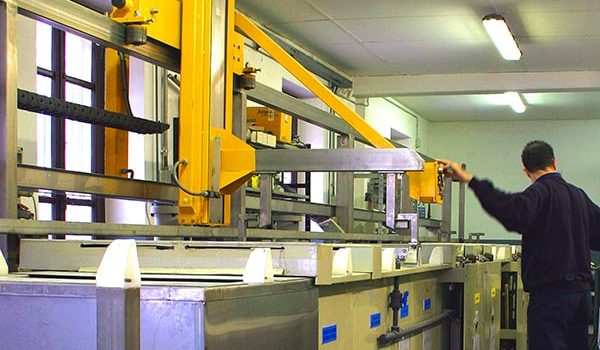
The advantages of silver coating an electrical contact are mainly improvement of conductivity and resistance to corrosion, with the subsequent benefit on its life span and performance.
Celsia’s galvanisation process has 3 phases:
1. Preparation of the surfaces to be treated
So that the coating adheres properly and has a long life span, it is important that the surfaces to be treated are free from oil and grease or oxidation and rust. Preventive cleaning of the parts to be treated is carried out with degreasing and pickling procedures.
Both of these processes are carried out in tanks aligned in sequence in the galvanic line, and are conducted with biodegradable solutions at room temperature. In addition to a caustic soda tank, to ensure a better result Celsia has added some cleaning tanks filled with custom-designed liquids, which thoroughly degrease and pickle every component before the coating phase.
The time the components remain inside the tanks is calculated based on the geometry of the part to be treated: the more complex it is, the longer it stays immersed in the liquid.
2. Coating
Once the surface has been prepared, the part to be treated can be put into the subsequent tanks, where the metal coating is applied by electrochemical effect.
For this phase Celsia has designed and developed special frames on which the products are placed during immersion in the liquid. This solution, while ensuring the parts to be coated are perfectly aligned with the anodes (electrodes), provides a major achievement in terms of quality of the coating and repeatability of the process.
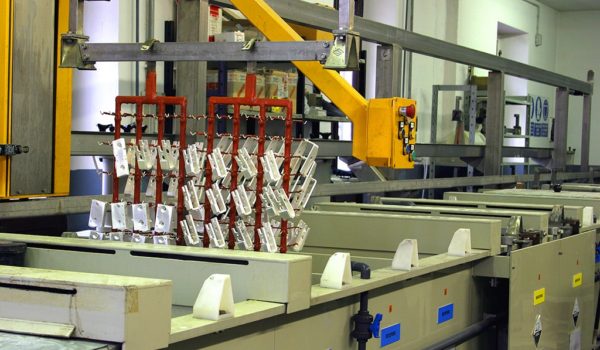
Celsia’s plant is automated and checked regularly both thermally, through temperature controllers in every tank, and chemically, with periodic analyses of the galvanic baths carried out by specialised companies, in order to verify the characteristics of the liquids. Hence customers are guaranteed constant quality of the electrolysis process performed on their electrical contacts.
Silver coating on the copper/tungsten components of an electrical contact and on ferrous materials does not adhere properly. To exclude these parts from the galvanisation process, Celsia has designed special insulating covers, produced with plastic extrusion technology. After the treatment these protections are removed easily, leaving the product in perfect condition.
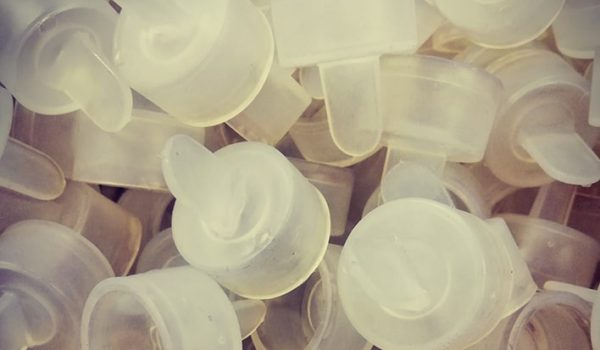
If the customer also requires the copper/tungsten component to be silver coated, it would first need to be copper plated. Celsia’s galvanic line also includes a tank for this treatment, which differs to silver coating only in that it uses copper anodes instead of silver ones. After the electrical contact has been copper plated, it can be completely silver coated.
In order to pay more attention to the environmental policies and fully comply with the requirements of ISO 14001, Celsia’s galvanic plant operates in a closed cycle, using carbon filters and underground silos to collect the liquids. Subjected to regular checks and periodic maintenance, it also has an indicator that electronically monitors the quality of the liquids by sampling the Ph.
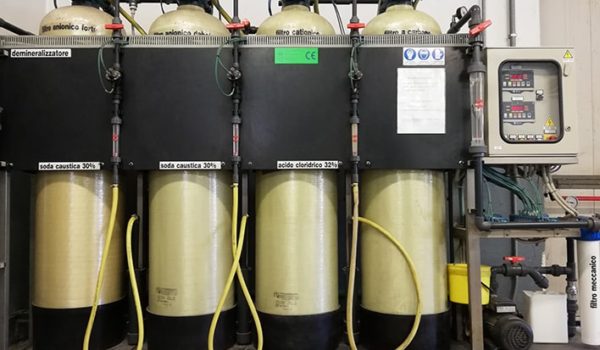
3. Finish and checks
When the parts have been coated, they are quickly dried to prevent patches of moisture from forming.
Using the Fischer Couloscope, Celsia checks and certifies the silver coating thickness of every production batch, discernible in flash silvering (1-3 microns) or silver coating (according to the customer’s request).
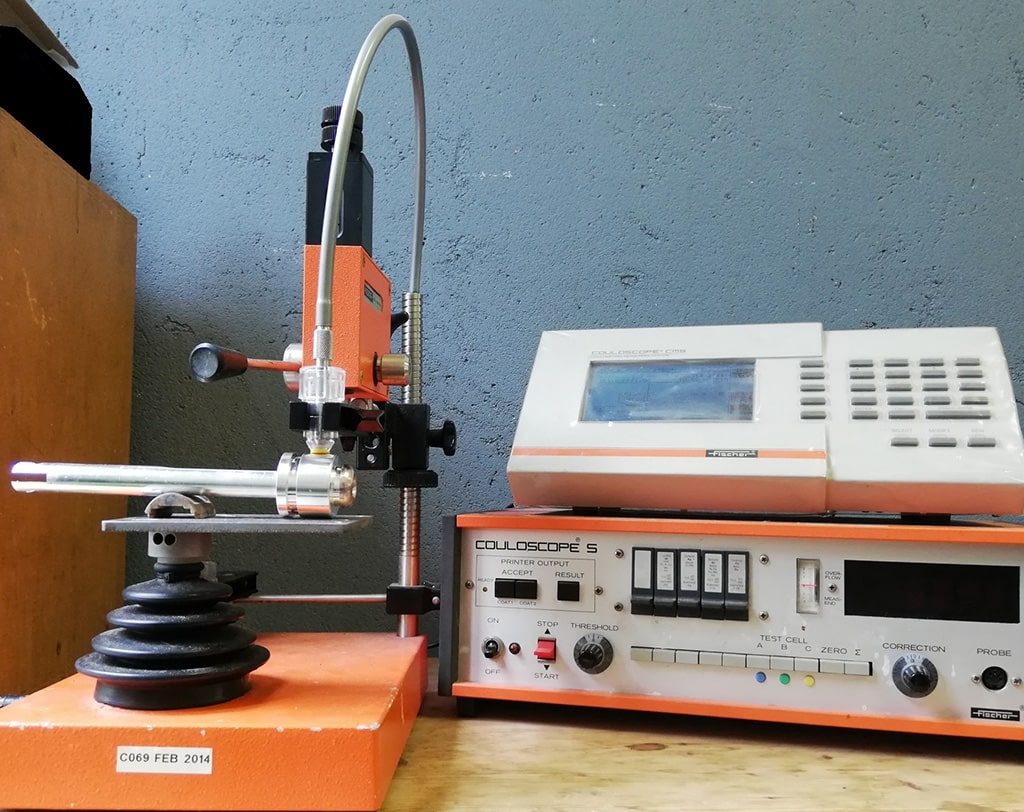
At the end of these 3 phases Celsia’s electrical contacts are ready for sale, suited to meet an increasingly demanding market in terms of quality and performance of the product purchased.